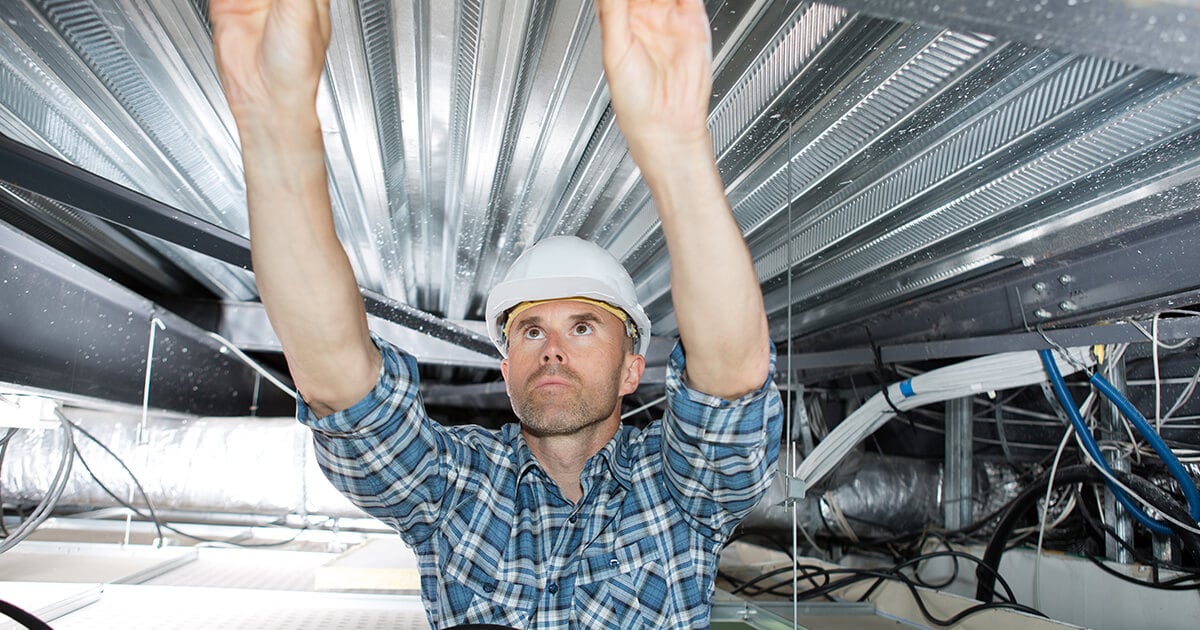
What’s the difference between 97 and 99.9? If you said 2.9, you’re only partially correct. When it comes to the successful implementation of retail store technology, the difference between an IT solution provider with a 97% first-time project success rate and one that delivers 99.9% can amount to thousands of dollars. It costs retailers both in the direct cost of troubleshooting and repairing problems that emerge from an error made along the way, plus the impact of delaying the project and missing out on the benefits of the new technology. Anyone who has witnessed a big store tech deployment derailing knows how painful it can be.